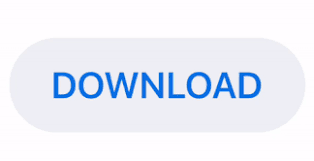

The brown object is a surface fit through the remaining material in the topology optimization mesh. 10 shows the topology optimization result. If we demand a very small minimum feature size, then the mesh must be able to represent the resultant configuration-which could mean a large number of elements.įig. The other consideration is the number of elements. The most efficient designs have more distributed material. If this is set very large, then the structure becomes chunky and the volume fraction target may not be achievable. This could be a goal-to seek a more organic type of shape. If this is set very small, then we allow “filigree” strands of material. There are two considerations here from a design point of view, there will be a minimum practical feature size. The minimum feature thickness is set at 0.25 in. Stress is expressed as a Factor of Safety and is a global measure. I also did a parallel study that used the minimize mass option as an objective with stress as a constraint. There is no constraint on stress or specific deflection values.
#Altair solidthinking inspire full#
I could then quickly sweep through a full range. I found this useful once I had explored some of the configurations produced by various Volume Fractions. The direct input option below the fixed radio button percentages allows for custom percentages, and also, by stringing values together, a batch of runs. The target design space volume (Volume Fraction) is 30%. The optimization objective is to maximize stiffness, in other words, to find an efficient design. Lattice is one of the new features in 2018. Other options are Topography, Gauge and Lattice. Too thin and the element size will be prohibitively small, too large and the non-design region will dominate the topology configurations.įinally, it’s time to go and optimize! I set the optimization Type to Topology. An annular ring is partitioned as a separate body by offsetting the hole surface. The Partition Icon is used to achieve this.

I am loading the inside of the hole, so the material immediately abutting the load must remain intact by designating it a non-design space. The new faces created by the line intersections are then pulled through the body using the Push/Pull icon, creating an extruded cut. Two lines are snapped to the corners of the surface. By clicking on the line feature in the Points/Lines icon, a sketching toolbar appears. Inspire has some neat tools to do this within a versatile geometry creation and manipulation set. I want to slice the corners off of my initial design space to make the topology search more efficient as described. It is a good idea to make this kind of assessment of design space, maybe even to try a set of exploratory FEA studies on broad design space options to understand useful limits.

So, my width limit skews the resulting configuration. The bending load case would naturally want a wide base to provide the biggest reacting couple. In this lug, the width is a controlling factor. Conversely, if too much material is clipped from the initial design space, then the final configuration can be skewed away from a more “natural” result. If the redundancy is removed, then 50% Volume Fraction is literally attacking the meat of the problem in the 10 cubic inches of design space left. A tighter initial design space can be defined and has the advantage of reducing the element count in the underlying FEA and making the target Volume Fraction reduction more focused on critical material.Ī 50% Volume Fraction used on 20 cubic inches, with 10 cubic inches is redundant and is not effective in driving toward a useful configuration. From engineering basics, a lot of the material is not needed above the hole.

The lug will carry axial loads and side loads. The vertical part is the design space the base is a non-design space. My objective was to create a lug-like configuration starting from the geometry shown in Fig. 5: Initial design space, loading and constraint.
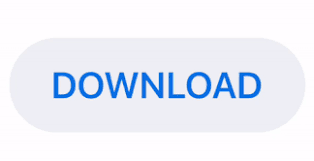